What’s Lostwax ?
ロストワックスとは
ロストワックスはロウを利用した鋳造方法の一種です。 ロストワックスの作り方は、まず、加工が簡単な蝋(ろう)で原型(マスター)を作ります。原型を砂、石膏、セラミックなど台材に仕込み、蝋を溶かして焼き固めたものが鋳型になります。できた空洞に溶融金属を流し込み、材料が冷え固まったら型を割って製品を取り出し完成です。いくつか原型を組み立てる(ツリーと言います。)ことで複数取りを可能にします。 また、量産の場合には、原型を作成するための金型を製作します。 ロストワックスは寸法精度が高く、鋳肌がきれいでステンレスや炭素鋼などいろんな材料で鋳造できることが大きな特徴です。
Lostwax Work
ロストワックスのことなら武杉製作所へ
武杉製作所はロストワックス鋳造を主力とした会社です。 横浜の本社を拠点に海外にも拠点を持ち、台湾工場(台湾武杉)を始め中国・ベトナムで加工しています。 すべての製品の組立・検査・検品を日本で行い、ほぼ完成品の形でお客様に納品しています。 業用金物業界のトップメーカー、タキゲン製造株式会社様のトップサプライヤーとして半世紀近くにわたり実績を積んできております。 その他様々な業種・業界の企業様にご愛顧頂き、多岐にわたる製品の製造を行ってまいりました。 高い寸法精度を求められるものや複雑形状の製品など、これまで培ってきた技術とノウハウで、より高品質な製品提供を目指して努めてまいります。
Specialty
武杉のロストワックスの強み
1
簡易金型による少量(100個)からのロストワックス鋳造
一般的に、ロストワックス鋳造を行う際にはロット数数千個~数万個/程度がないと、大手メーカーは製作には携わってもらうことが難しいといえます。一方で、武杉製作所では少量の生産でも鋳造で行いたいというお客様のご要望にお応えし、数百~数千個の製品でのロストワックス鋳造に対応しています。アルミ簡易金型によるイニシャルコストの低減を含め、少量生産に実績と多数のノフハウを蓄積していることで実現できる、武杉ならではの強みと言えます。また、量産に向けたの試作開発にも社内設備を用いて対応しております。
2
一貫生産体制による完成品での納品が可能
ロストワックス+切削+仕上げ加工+組み立て+検査まで社内一貫対応が可能なため、お客様の求める完成品での納品が可能です。
3
グローバル生産拠点による量産対応
台湾・中国を始めとしたグローバル生産拠点を保有しており、大量生産の対応が可能です。
4
安定品質・迅速で柔軟な対応
国内での切削・組み立て・検査により「常に安定した品質」「トラブル時の迅速かつ柔軟な対応」が可能です。 武杉製作所で受注した製品はすべて、国内の厳しいチェック体制のもとで検品を行い出荷しています。 量産のため海外の提携工場で製造された製品についても、すべて国内の本社にて検品を実施。厳格なチェックにより、クオリティの高い製品のみをお客様にお届けしています。
5
製品開発の設計段階から協力可能な生産体制
3Dプリンターによる形状確認、切削及びロストワックス製法(金型無し)による試作、ロストワックス(金型製作)による量産まで可能です。 お客様の製品開発のスタートから完成までトータルでサポートいたします。
幅広い業界で採用されるロストワックス
ロストワックスは、航空機、船舶、自動車、精密機器、産業機器、医療・介護、建築と数多くの産業に採用されています。 例えば下記のような製品に使われています。
・配電盤
・分電盤
・特別装備車両
・産業機械
・自販機
・エンジンのターボチャージャー・タービンブレード
・ゴルフクラブヘッド
・指輪など宝飾品
ロストワックスの特徴
ロストワックスは非常に優れた特徴を持つ鋳造方法です。
3次元曲面や複雑形状が得意(形状の制限があまり無い)
切削加工では難しい3次元形状や複雑形状も容易にでき、自由なデザイン設計が可能です。
薄肉、厚肉どちらにも対応
溶融温度が高いため、ダイカストでは難しい厚肉も可能です。
寸法精度が高い
金属の収縮率をコントロールすることで寸法精度を高くすることが可能です。さらに寸法精度を求める場合には機械加工を対応を行うことができます。
鋳肌が美しい
従来の鋳造方法に比べ、仕上がりがキレイで、用途によっては表面処理せずそのまま利用もできます。さらに、鏡面研磨やヘアライン研磨をすることで光沢仕上げ等が可能です。
製品強度が高い
一体部品として鋳造することで、組み立て・溶接等による部分強度の弱点の克服が可能です。 鋳造でリブを入れたりすることで、さらに高強度にすることが可能です。
他の成形用金型と比べ金型費が非常に安価
一般的な金型(プレス、ダイカスト、射出成形など)は数百万する金型も多いですが、ロストワックスの金型は数十万程度の金型費で量産が可能になります。また、ロストワックスの金型は耐用年数が非常に長く原価低減に寄与でき、さらに、同じ金型で鋳造材料を変更することも可能です。
上記特徴を踏まえたロストワックスのメリット
ロストワックスなら一体物の鋳造が可能です。複雑形状品をパーツごとに製作し、追加工、溶接、組み立てを行っていたような製品からの工法転換が可能です。そのため工程をできるだけ減らした製造でコストダウンに寄与できます。また、溶接、組み立て等の部分強度の弱点克服も可能です。
試作段階では金型不要の3Dプリンターから鋳造を行います。 量産時と同じ条件でのテストが可能です。その後、試作にて形状確定した段階で金型を作成し、そのまま量産体制に移ることができます。試作と量産が同じ製造方法のため、仕様、設計変更の必要がなくスムーズな移行ができます。 切削加工品の場合は、ロストワックスと同様に試作から量産まで対応可能ですが、金型を作るわけではないため、量産時のコストメリットが出しづらいという問題があります。
切削の場合、利用する工具(基本的には直線形状)が届く範囲が加工可能範囲となり、中空形状は加工原理的にできません。ロストワックスは形状の自由度が非常に高く、従来の加工原理にとらわれない製造が可能です。他の加工方法では実現不可能だったものがロストワックスならできるかも知れません。
ロストワックスは様々な可能性を持った加工方法
コスト低減・軽量化(除肉による)・デザイン性向上・強度アップ
Before
ブロック材からの削り出し
After
ロストワックス+追加工
Before
複数部品の切削+組み立て (溶接・圧入等)
After
ロストワックス+追加工
Before
板金加工+溶接
After
ロストワックス
Before
砂鋳物+研磨
After
ロストワックス
ロストワックスの弱点・デメリットは?
- 切削やダイキャストにくらべ精度は低い
ロストワックス一般的な公差は 25mm~50mm の大きさで ±0.4mm と言われています。
武杉製作所では気温湿度等の条件を徹底してコントロールすることで±0.2mm~0.3mmらいに収まる公差が可能です。 - 1個〜10個程度のボリュームには向きません。
型を作るため、コストが割高になりその後の量産想定が無い1~10個のみの製作には向いていません。
ただ、3Dプリンター+ロストワックスで複雑形状が可能で、この場合、切削ではできない形状の製品が製作可能なため、少量でもメリットとなります。 - ダイカストと比較した場合に型の寿命が短い
ロストワックスの金型は一般的にはアルミ型を利用するため安価な反面、金型寿命が短いと言われています。
武杉製作所では数が多くなる場合、金型を一部鉄型にして強度をもたせることで、アルミダイカスト金型と同等程度の寿命が可能です。
Lostwax Process
ロストワックス生産工程
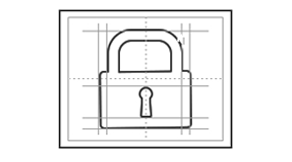
step 01
図面設計
お客様のご要望を打ち合わせや図面等でいただき、ロストワックスに適した設計を進めていきます。
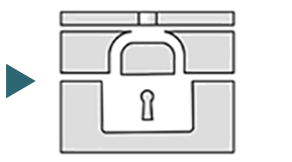
step 02
金型製作
図面をもとに金型(基本的にアルミ型)を製作します。ロストワックスの収縮率は物品等によって変わるため、新規で製作する場合は金型サンプル品を提出してからの稼動となります。
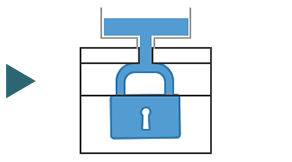
step 03
インジェクション
金型にワックスを注入し、製品と同形状のワックス模型を製作します。射出成形機と同じイメージで、成形には半自動で行います。

step 04
ワックスの修正
ワックスにバリなどがないかを、目視にて検査します。
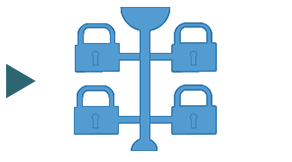
step 05
ツリーの組立
樹木のようになっていることから、この名称がつきました。メインの湯口棒にワックスを取り付けます。形状によって、一つのツリーで作られる数量は変わります。
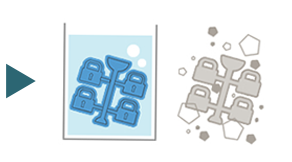
step 06
コーティング
作成したワックスツリーに耐火材をコーティングします。コーティングと乾燥を5~7回繰り返し行いコーティング層を厚くします。室温・湿度管理が重要です。
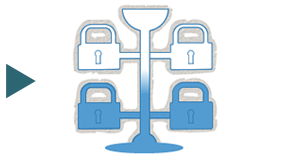
step 07
脱蝋
ワックスにコーティングが完了したツリーに加圧・加熱し、鋳型内部のワックスを取り出します。ワックスが溶け出した耐火材が製品の鋳型になります。
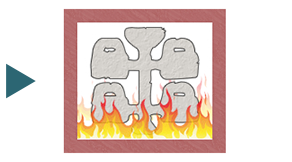
step 08
焼結
図鋳型に耐熱強度をさらに与えるために高温で焼きます。焼結は、鋳込み時の鋳型の割れ防止や湯回りを良くするために行われる重要な工程です。
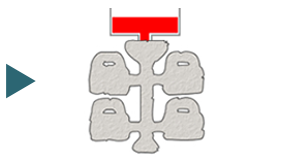
step 09
鋳込
焼結した高温の状態の鋳型に。溶解した金属の鋳込みを行います。鋳込み前に鋳造炉から不純物を取り除いた状態のものを鋳造します。
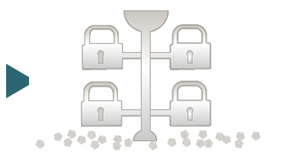
step 10
型ばらし
鋳込みが完了した鋳型を振動機を使用して破壊し、ツリー状の製品を取り出します。
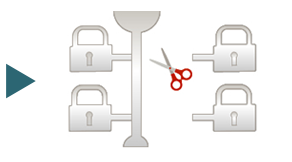
step 11
カッティング
高速カッターを使用し、ツリーから製品を一つ一つカットします。
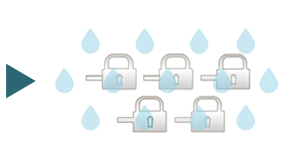
step 12
ショットブラスト及び酸洗
カッティングした製品に細かく残っているシェルに酸洗とショットブラストを行い、細部にあるシェルを完全除去します。
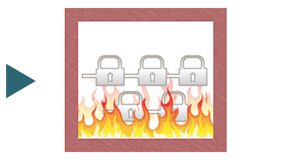
step 13
熱処理
ご指示をいただいた製品については、固熔化熱処理を行います。組成を安定させるのが目的です。
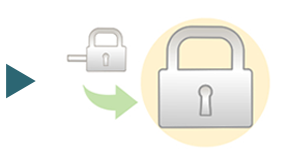
step 14
表面処理
ベルトサンダー等で湯口仕上げを行い、サンドブラストで面を平らにします。
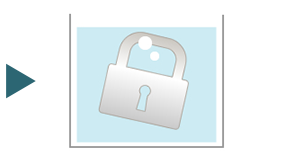
step 15
酸洗い
製品についている不純物を除去します。
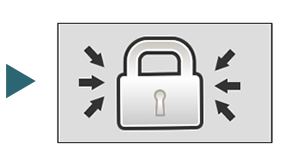
step 16
矯正処理
鋳造時の歪を除去するために油圧プレスにて整形を行います。
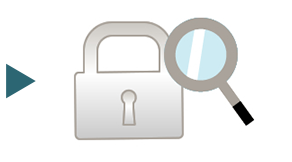
step 17
検査
1チャージごとにテストピースを用意し、成分分析を行います。それぞれの規格内に入っていることを確認します。
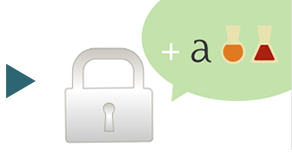
step 18
2次加工
ご要望に合わせて電解研磨等を行います。ヘアライン研磨・鏡面研磨などの研磨工程の場合には後工程にて対応します。また、ご要望に合わせて表面処理を進めます。
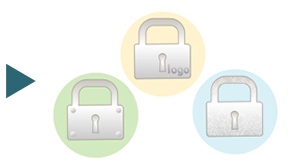
step 19
穴あけ加工等
穴あけ加工、タップ加工、CNC旋盤加工、マシニング加工など、ご要望のスペックに合わせて追加工を進めさせていただきます。
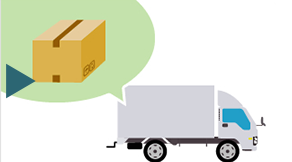
step 20
完成
完成した鋳型をご指定の場所へ納品いたします。
ロストワックス対応可能な材質
溶融金属全てに対応 鉄、ステンレス、アルミニウム、銅、チタン、マグネシウム、亜鉛
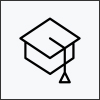
ロストワックス製法による製品例
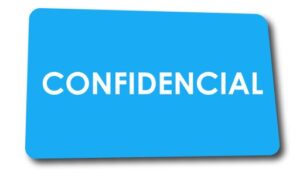
SUS製ダイヤル南京錠
このダイヤル式南京錠は中でも珍しく、素材はSUS304相当のSCS13でロストワックス製法にて製作しています。ダイヤル部などには焼結品を彫刻切削にて文字を掘っております。また、南京錠は摺動箇所などの寸法管理が大変厳しくロストワックスの鋳出し寸法では絶対に対応できません。そこでM/Cや追加工を施します。当製品も、勘合部品として弊社にて組立・調整・梱包と最終工程まで行わせて頂いております。
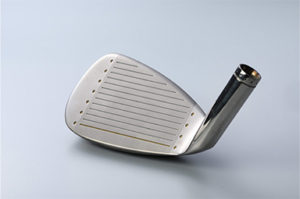
ゴルフクラブヘッド
ロストワックス製品ではゴルフクラブのような複雑異形形状の製品も製作可能です。 ただし、ゴルフクラブのように硬さを求められる製品はSCS13など(SUS304相当)では硬度が足りません。そこでSUS630相当である17/4-PHでの生産対応となるのが通例です。
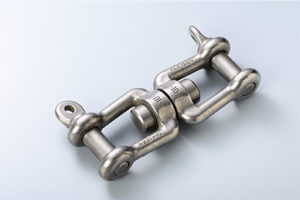
チタンシャックル
ロストワックス製法によるチタン製品も対応可能です。チタンは強度及び耐食性に大変優れており、高付加のかかるシャックルなどにも用いられます。 ただし、強度を求められている製品の為、またご要望に応じて目に見えない巣を発見する為、この製品は全数レントゲンで内部検査及び抜き取りで破壊試験を行い出荷させて頂いております。
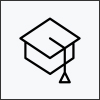
ロストワックス予備知識(精密鋳造の歴史)
古代メソポタミアに発明されていた鋳造は、太古より用いられてきた加工方法です。 年代については諸説ありますが、古代メソポタミアの青銅器に蜜蝋を原型として用いる加工法が既に発明され、それがロストワックスの始まりと言われています。日本にも弥生時代に中国を経由して仏教と供に入って来ました。この加工法をもとに、銅鐸、銅鏡、刀剣など宝飾品や武器が作られるようになり、奈良時代になると多くの仏像や梵鐘が作られました。 明治時代以降、工業製品用に複雑な形状の鋳造品の需要が高まり生産数が増え、第二次世界大戦中にはアメリカの戦闘機用過給機(ターボチャージャー)が量産され技術が発展し現在に至ります。