金属製品の試作から量産まで最適な加工方法をご提案
武杉製作所では、試作の必要個数や形状をお伺いした上で、量産を見越した最適な試作加工方法をご提案します。
3Dプリンタ | 切削 | 板金 | ロストワックス |
金型レスの試作向けロストワックスで製品開発支援
3Dプリンタとロストワックスの組み合わせなら量産を、量産を見越した開発が可能に
このようなご要望にお応えします
・イニシャルの費用を抑えたい
・短納期で金属の試作品を作りたい
・形状が数パターンあり、実際の素材でテストしてみたい
・強度テストをクリアしてから量産(金型製作)をしたい
・量産の前にデザイン・形状を確認したい
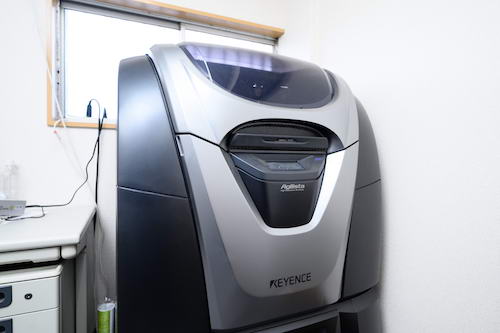
3Dプリンター
どんな技術??
ロストワックス精密鋳造はワックスを用いて原型を製作し、その原型を元に鋳型を作る鋳造方法ですが、そのワックス原型部分を3Dプリンタで製作して鋳型を作る技術です。
そのため金型を使用せずに様々な形状、素材をつくることが可能となり、試作段階のコストと納期を抑えることが可能です。また、実際に量産に移行した際にもロストワックスの工程がそのままシフト可能なため、量産を視野にいれた試作開発に向いています。
材質について
アルミ、銅合金、鉄、ステンレス、チタンなど幅広い材質に対応しています。量産時と同材質での試作を行うことが可能ですので、試作から試験、量産までスムーズに進みます。
形状について
3次元複雑形状も製作可能で、複数パーツを一体化して製作することも可能です。
寸法について
3Dプリンタの精度に左右されるため、通常のロストワックス工法と比較すると精度は劣ります。そのままの状態だとデザイン、形状確認、量産と同材質での試作といった位置づけになりますが、寸法精度が求められる際には機械加工により対応可能です。
面粗度について
3Dプリンタ造形品の精度に左右されます。金型で製作した製品とは若干異なります。ただし、意匠面に関してはご要望により表面処理にて対応可能です。
納期について
金型を使用しないので、通常のロストワックス工法よりも短時間で試作品を製作可能です。
金属の試作方法を比較
金属製品の試作の主な加工方法は以下の手法が挙げられます。
加工方法 | 特徴 |
---|---|
板金加工 | 板材を曲げ、切断、溶接、穴あけ加工、レーザーなどの加工で製品に仕上げる方法。形状にもよるが他工法と比べると安価に試作することが可能。加工できる厚さに制限があるが、大きい物も対応可能。 精度:△ コスト:〇 納期:〇 量産:△ |
切削加工 | ブロック材から製品を削り出す方法。高精度品の製造が可能であり、材質も幅広く対応可能。形状や材質によっては難しい場合やコストが高くなる可能性がある。 精度:〇 コスト:△ 納期:△ 量産:✕ |
ロストワックス (樹脂3Dプリンタ) | 3Dプリンタで原型をつくることで金型を使用せずにロストワックスの試作を行うことが可能。3次元複雑形状でも製作可能で、複数パーツを一体化させて製作することも可能。面粗度、寸法精度は金型を使ったロストワックスに比べると劣る。 精度:△ コスト:△ 納期:〇 量産:〇 |
金属3D プリンター | 作れる材質が限られるが、チタン等の難削材も可能。他工程では無理な形状も対応できるが1個あたりのコストがとても高い。また、精度は3Dプリンタに依存するためまだ発展途上といえる。 精度:△ コスト:✕ 納期:〇 量産:✕ |
量産を見据えた試作の重要性
試作時の注意点の一つとして、試作をクリアした後の量産検討時に、コストを抑える加工方法が選択できるかどうかが問題となります。
試作と量産の加工方法が異なる場合には再度試作が必要です。
試作から量産に移行した際のコストメリットについて
板金
コストメリットを出すには金型を製作する必要がありますが、形状によっては対応が難しい場合があります。
切削
そのまま量産に移行する場合はあまりコストメリットがでない場合があります。
ロストワックス(樹脂3Dプリンタ)
ロストワックス工法にそのままシフト可能で、試作段階から量産を視野にいれた開発が可能です。量産時には金型を製作するので量産によるコストメリットが狙えます。
金属3D プリンタ
製作できる個数が3Dプリンタの造形エリアに依存する為、大きさにもよりますが試作段階とほぼコストは変わりません。
金属加工法を選ぶ際に考慮すべきこと
金属加工法には様々な加工法があり、それぞれに長所短所が存在します。では、加工法を選択する際に何を考慮し、何を選択すればよいのか、加工法を選ぶ際に考慮すべきポイントをご紹介します。
加工コストと生産性のバランスを考慮する
金属加工は製品の要件や予算に応じて、加工コストと生産性のバランスを考慮する必要があります。
単品、小ロットの場合は金型を必要とする加工法の場合はコスト面で不向きですが、ロット数によっては鋳造やプレス加工などの大量生産向きの加工法を選択することでコストメリットがでます。
また、工作時間の最適化など、コスト削減や効率化の観点から考慮することも大切です。例えば、複数パーツを組み立てる必要のある製品の場合、鋳造法で一体成形することで加工工数を削減し納期短縮、コストダウンにつながる場合があります。
製品の形状とサイズに基づく加工法の選択
製品の形状とサイズは非常に重要な要素です。
一般的に複雑形状の製品には、CNC加工などの精密加工法が適しており、高い精度と細かなディテールを実現することができます。
しかし1個あたりの加工コストは高くなるため、ロット数が多い場合は鋳造法など量産に適した形状を選択した方が納期、コストともにメリットが出る場合があります。
一方、単純形状の製品の場合は、鋳造よりもプレス加工や旋盤加工などの高速生産が可能な加工法の方が適している場合があります。
製品の材質に合った最適な加工法の選択
製品の材質も加工法を選択する上で重要な要素となります。
例えば、チタンなどの難削材は機械加工だと加工コストが高くなるためロット数が増えるとその分コスト高になりますが、ロストワックス鋳造法であればロット数が増えるほどにコストメリットがでます。
一方、アルミニウムなどの比較的軟らかい材料に対しては、プレス加工や押出加工などの成形加工が適している場合があります。
製品の材質に合った最適な加工法を選択することにより、加工効率や製品品質の向上が期待できます。
まとめ
材質、形状、サイズ、生産数など、製品の要件に合わせて加工法を選択することで納期短縮やコストダウンが可能となりますが、すべての加工法を把握することは非常に難しいことです。
武杉製作所ではロストワックス鋳造法を元に今まで培ってきた技術・知識を活かし、皆様の課題に対し最適な技術提案をさせていただきます。
製品開発、工法転換、で悩みの方はご相談ください。